Optical 3D measurement technology for high point density and accuracy in all phases of production
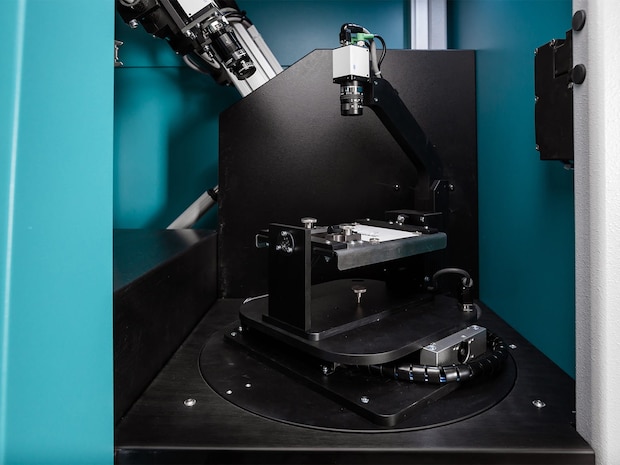
Optical measurement technology in use
The high-resolution scan data is capable of being compared directly against a CAD model, or used for dimensional, shape, and positional tolerance measurements. With object point resolutions down to 5 um, as well as our smart multi-image referencing using virtual targets, the FLEX-3A is ideally suited for high-precision automated 3D inspection of complex small parts.
Optical 3D metrology at a glance
High precison and high resolution scan data
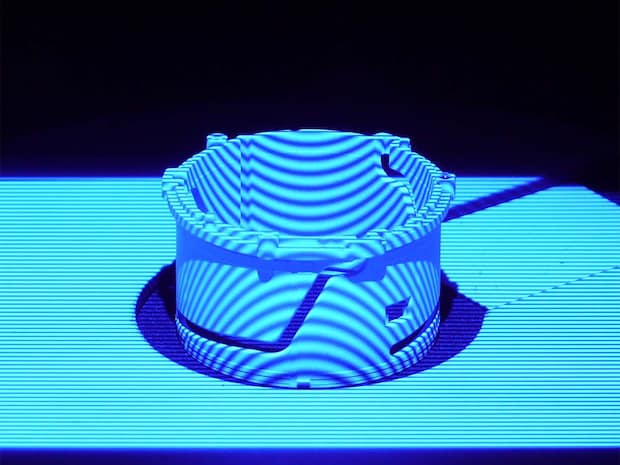
Stereo camera resolution up to 12 million px
- Camera resolution up to 12 million px
- Measuring field sizes from 20mm to 230mm
- Blue light projection technology
- Photogrammetric image referencing with smart camera
- Up to 4 moveable axes
Industrial measurement technology and accuracy
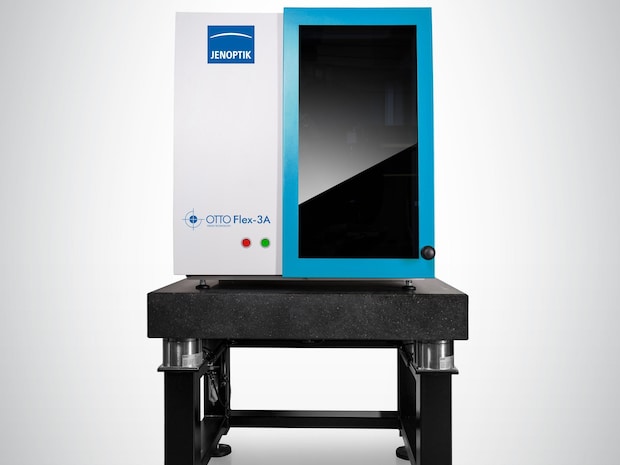
Closed industrial housing
- Closed industrial housing
- Traceable measuring accuracy
- Calibration monitoring and automatic recalibration
- Vibration isolation
- Windows 10© operating system
Automated scanning and reporting
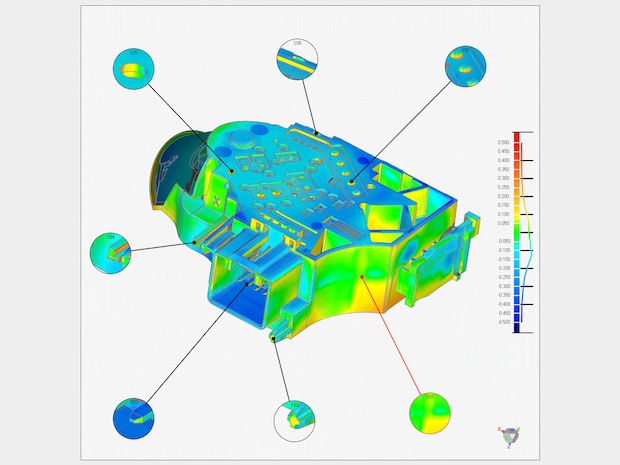
Colored comparison of actual to target models
- Direct comparison to CAD as well as inspection of dimension, form and position
- Parametric test job creation
- Fully automatic worker self-testing
- Easy test plan creation with one click
Find the right product for your application
Optical 3D scanner for automated inspection
The 3D scanners of the FLEX-3A series are suitable for first sample and prototype inspection, as well as automated random sample inspection during production.
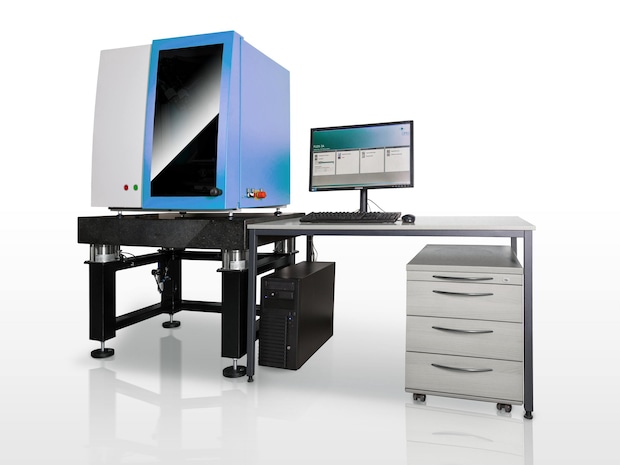
FLEX-3A
The FLEX-3A utilizes a closed housing concept, that when combined with complete automated data acquisition, calculation and evaluation, helps ensures long-term stable system calibration and operation under production conditions.
The use of an object fixed reference camera enables highly accurate and automated photogrammetric combination of partial views into one complete 3D model, with no need for registration targets.
Two integrated motorized axes by standard can be supplemented by additional axes and motion sequences as necessary.
Benefits
- Small measuring fields up to 20 mm object field size
- 5-12 million pixel stereo camera resolution
- Modular measuring field change
- Highly accurate measurement results
- Multi-image recording without registration targets
- Digital projection with blue LED lighting
- Automation of data acquisition and evaluation
- Motorized object and sensor movement
- Motorization modular expandable
- Fully automatic sensor calibration
- Free and easy creation of scan plans
- Closed industrial housing
- Vibration insulation
- Measuring principles: triangulation, structued light projection, photogrammetry
Specifications | FLEX-3A/12M | FLEX-3A/5M |
---|---|---|
Available measuring fields | 20mm to 210mm | 20mm to 230mm |
Camera resultion | 12 Mio. px | 5 Mio. px |
Measuring point distances | 5µm - 50µm | 8µm - 90µm |
Size (WxDxH) | 855mm x 854mm x 930mm | 855mm x 854mm x 930mm |
Weight | approx. 145kg | approx. 145kg |
Operating system | Windows 10 | Windows 10 |
Power Supply | 230V / 50Hz / 5A | 230V / 50Hz / 5A |
Optional | Vibration insulation table with air-spring elements | Vibration insulation with air-spring elements |
Image capturing time | < 2s | < 2s |
Extensions of 3D metrology for industrial and customized solutions
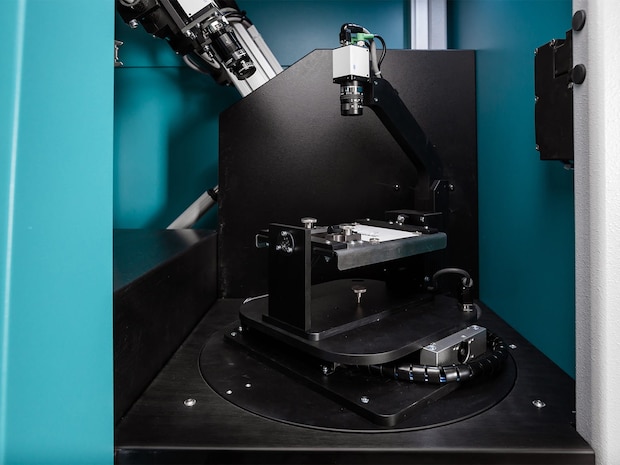
Automation by four axes
All aspects of integrating the FLEX-3A into your production line are handled directly by JENOPTIK, including, but not limited to:
- Integration of additional motorized axes
- Object specific brackets
- Robot based loading
- Automated part loading/feeding
- Integration into production lines
- Integration of individual 3D evaluation programs
- Combined solutions for 2D and 3D inspection tasks
- Complete automation of sampling/serial testing
Intuitive user interface and automated processes
FLEX-MAN system software
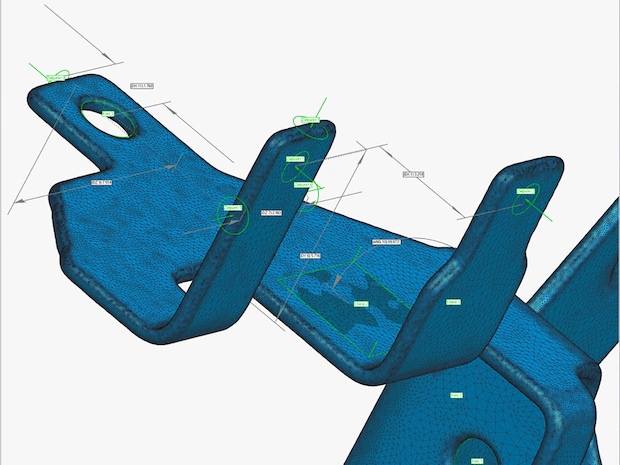
Software FLEX-MAN
3D digitization without registration targets
- Fast triangulation with high-resolution stereo cameras (up to 12 million pixels)
- Structured light projection method for area scanning with subpixel accuracy
- Fully automatic, photogrammetric registration of all partial views to a complete model
- Use of one or more reference cameras to create virtual registration targets
- Fully automatic optimization of virtual target number and distribution
Traceable measuring accuracy
- Equipment acceptance according to VDI guideline 2634, sheet 3
- Automated recalibration after measuring field change with one click
- Calibration monitoring
- User guided user interface for recalibration
Simple, intuitive operation
- Automated data acquisition from various directions
- Pre-configured with standard scan plans
- Infinite number of individual scan plans
- Simple setting of part-specific measuring positions, acquisition parameters or automation sequences
Individual automation options
- Direct start mode for worker self-test
- Support for automated, parallel 3D digitizing and inspection of multiple parts
- Support of manual, fully, or partially automated measuring processes
- Multi-level, macro based point cloud optimization
- Provision of interfaces for data transfer to statistical programs
Modularity
- Integration of additional motorized axes via plug and play
- Integration of remote controlled software evaluation packages
Product recommendations for optical measuring and testing systems
Do you have any questions?
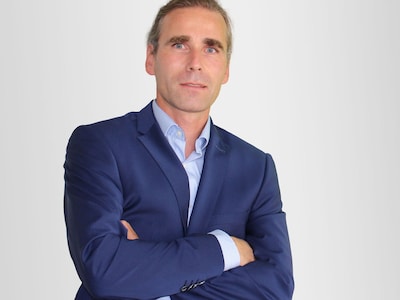