Test stations for the optical inspection of stamped parts
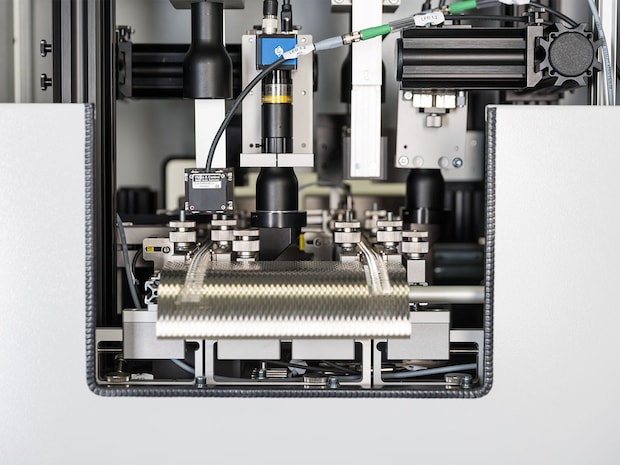
Use of our double track test stations
The demands for efficiency and cost structure in stamping production have grown rapidly. Manufacturers of stamped parts need competitive solutions that enable zero-defect production despite increasing process complexity.
PSS-40 test stations are an innovative leap from the traditional random test of stamped parts, to the fully automated in-line, inspection, measurement and sorting of stamped production parts.
Real-time delivery and processing of each manufactured part’s inspection data, from the first punching stroke onwards, allows shorter and more efficient changeover processes, high stamping line utilization, and the lowest possible consumption of resources. For our customers, this means improved quality at lower costs.
Our latest test station for punch strips of the PSS-40 series
Benefits at a glance
- Uninterrupted production of stamped strips with 100% quality
- No press stops for sporadic missing parts, waste, welding of raw material
- Space-saving stamping line configuration, no additional strip welding device
- Fully automated production, saves resources and time
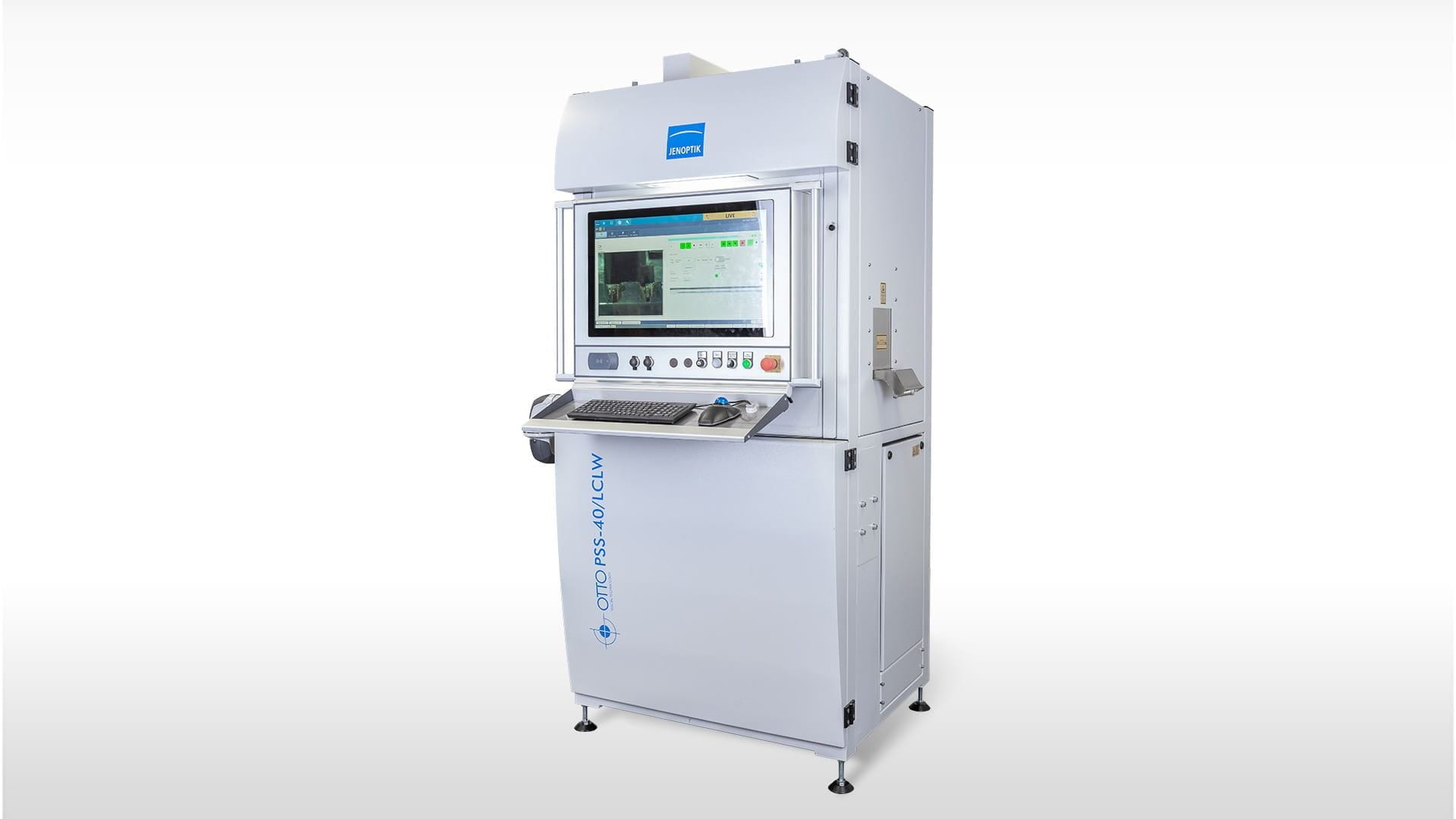
Special features LCLW
- Fully automatic tensile test after each weld
- Cutting out of first strips section for tool setup
- Cutting of strip sections or individual parts in the process
- Free of choice cutting/welding positions and cutting geometries
- Processing of multiple connections
- OVIS Inspect software with fully integrated laser configuration
Wear-free 24/7 sorting function of bad parts
- No wear and tear - Unlike mechanical cutting tools, a laser does not wear out
- High flexibility - No complex tool changes, simple flexible grippers
- Reduced changeover times
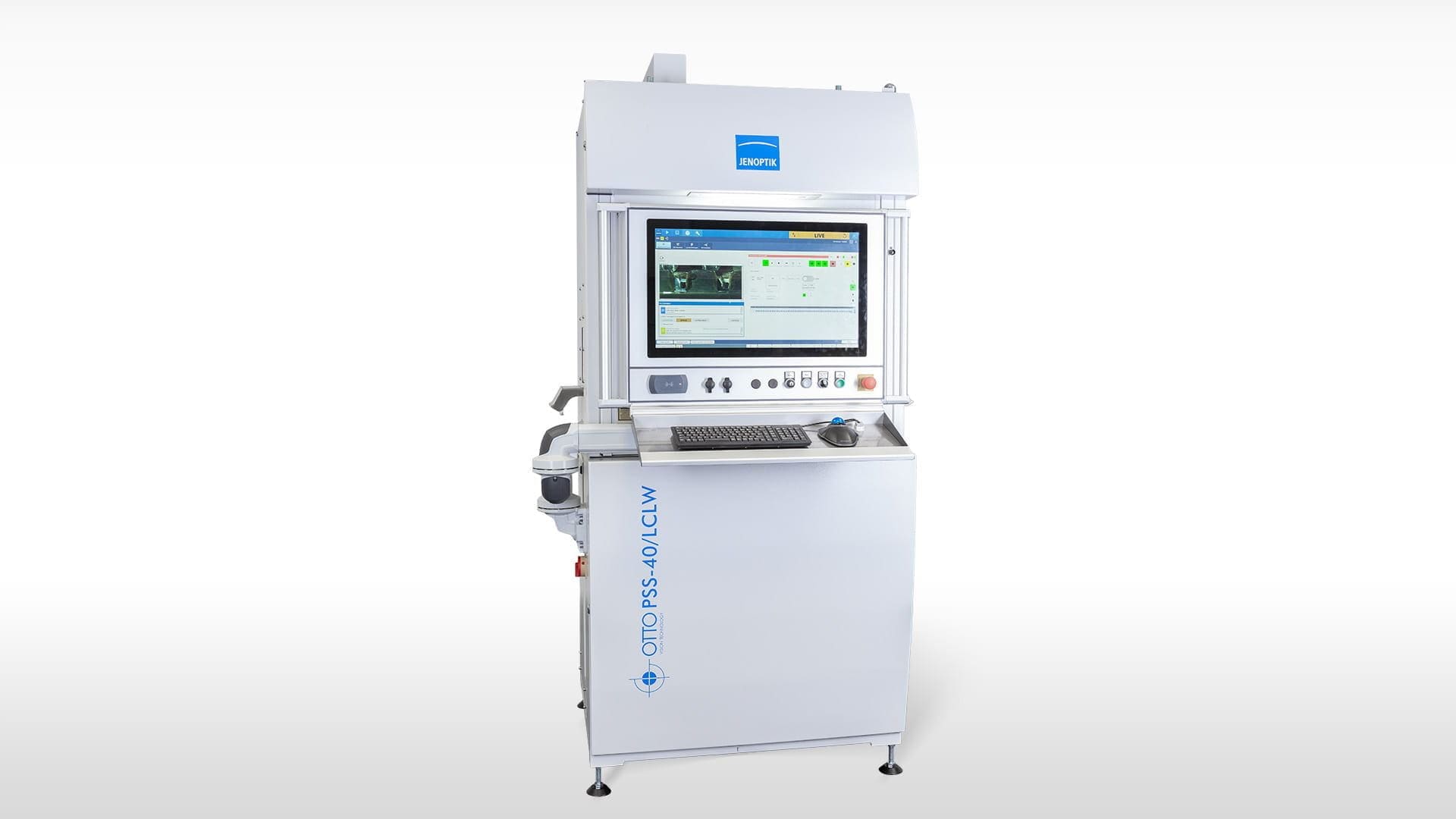
Our test stations at a glance
PSS-40/S
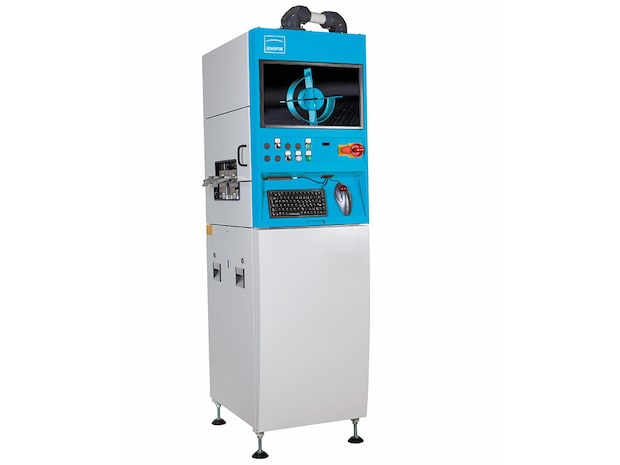
- Compact and space-saving design
- Usually use of 2 - 3 cameras
- Plate can be exchanged to the front
- Control unit direction-dependent
PSS-40/MH
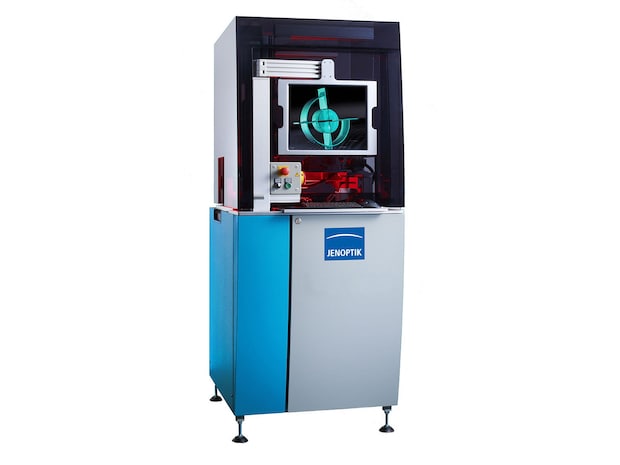
- Installation space for at least 4 cameras
- Plate laterally exchangeable
- Hood can be opened upwards
- Easy access for mounting and replacing the exchangeable plate
- Pivoting control panel
- Belt drive swivelling
PSS-40/LCLW
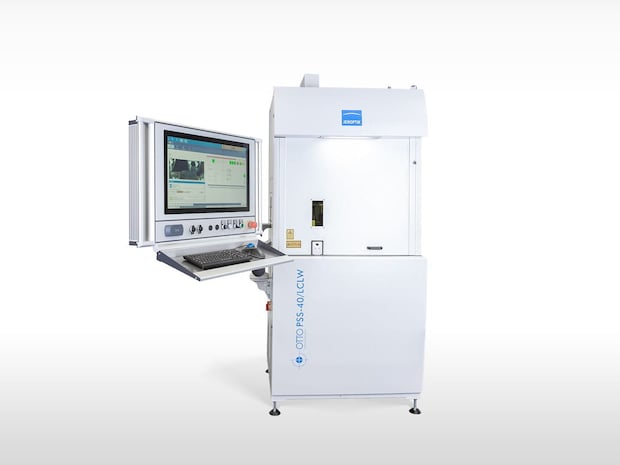
- High-speed inspection
- Laser cutting
- Laser welding
- 3-4 cameras
- LCLW pure for use with existing PSS-40 test stations
PSS-40/LCLW
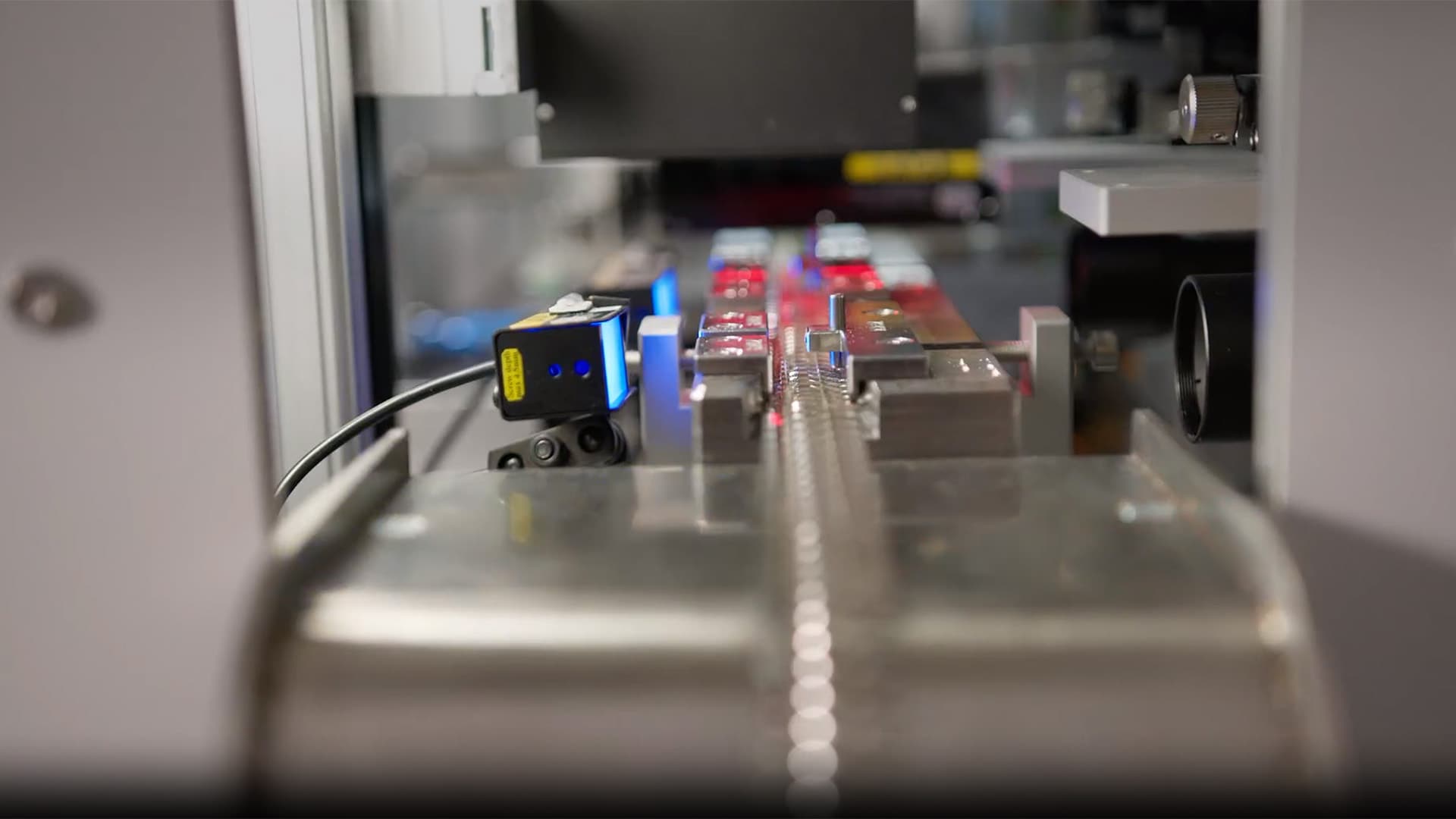
Find the right test station for your application
Loose parts - checking and sorting
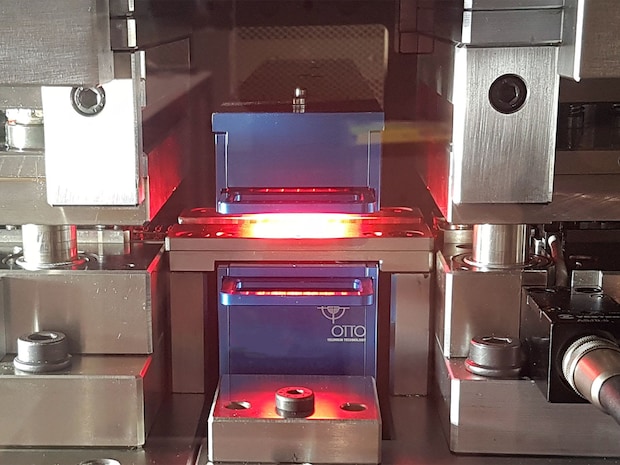
In-Die modules for testing
Advantages of our In-Die modules
- High-precision measurement, weld spot inspection, surface testing
- Considerable cost reduction compared to "traditional" test technology
- > 1800 stroke / min multiple falling
- Space-saving, encapsulated 1-camera system (< 60 mm space requirement in running direction)
- Image processing of the PSS-40
- Use of several modules with corresponding installation space
- Optional multiple cameras per module
- Applications in reflected and transmitted light
- SPS for controlling the separating station (optional)
Checking and sorting punched strips - PSS-40 Series
PSS-40/S | PSS-40/MH | PSS-40/LCLW or LCLW pure | |
---|---|---|---|
Width | 550mm | 810mm | 1250mm |
Depth | 900mm | 1000mm | 1290mm |
Height | < 2.100 mm | 1920 - 2700mm | 2230mm (2250mm with open lift door) |
All test stations are also available in adapted versions for the European, Asian and American continents.
Stamped strips and raw strips in the electroplating

Test station galvanic PSS-40
- Easy integration into the electroplating production line
- Strip guide on rolls
- SPS for tracking faulty parts
- Use in electroplating and bimetal production
- Use of standardized image processing software
- Geometry check
- Surface Inspection
- Use of monochrome and color cameras with appropriate lighting
Find more products
Please contact us, if you have any questions.
