Modular Beam Splitting System MBSS for efficient solar cell production
High-precision meets high-performance
The Modular Beam Splitting System (MBSS) simplifies the complexity of your overall system and offers an innovative solution for high-precision laser processing of perovskite solar cells (PSC). Through the perfectly matched combination of optics and micro-optics in a modular, easy-to-integrate design, the MBSS enables maximum flexibility and process stability.
In contrast to complex optical setups with mirrors and a multitude of individual components, the MBSS offers a ready-to-install and reliable solution and the parallel laser scribing ensures higher throughputs and increased productivity.
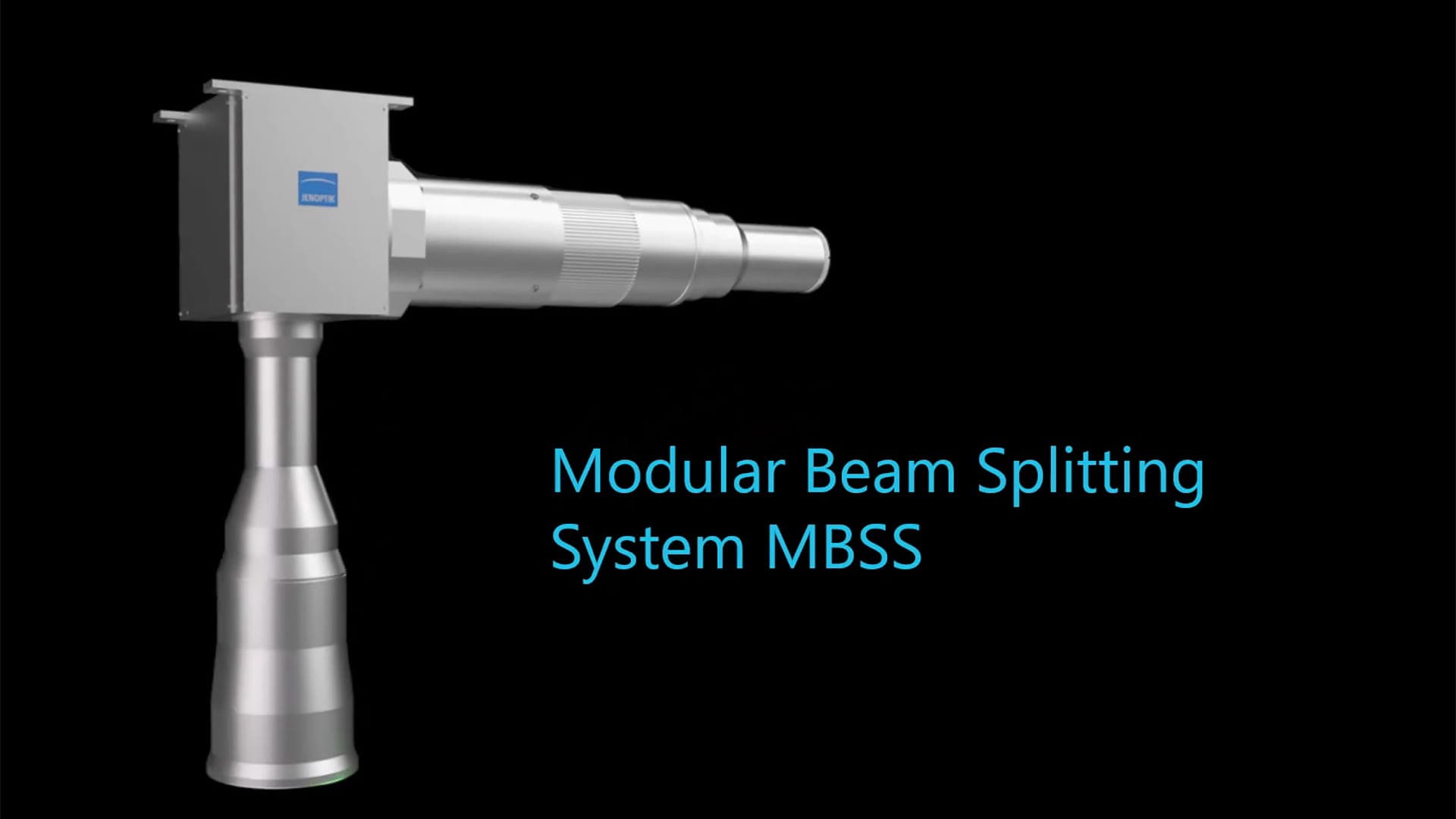
Stay flexible to keep your processes cost-effective
Concentrate on your core competencies and we will take care of the implementation of the optical setup. Simply select the desired parameters, such as wavelength, spot size and spot distance, and you will receive a fully assembled, ready-to-install optical module that offers you maximum process stability while remaining flexible. The design is such that parameters or hardware can be changed easily and without great effort. In addition, the MBSS weighs less than 10kg, making it ideal for on-the-fly processing on a conveyor belt, simplifying automation and minimizing dead time.
Reliable laser scribing process for Perovskite Solar Cells (PSC)
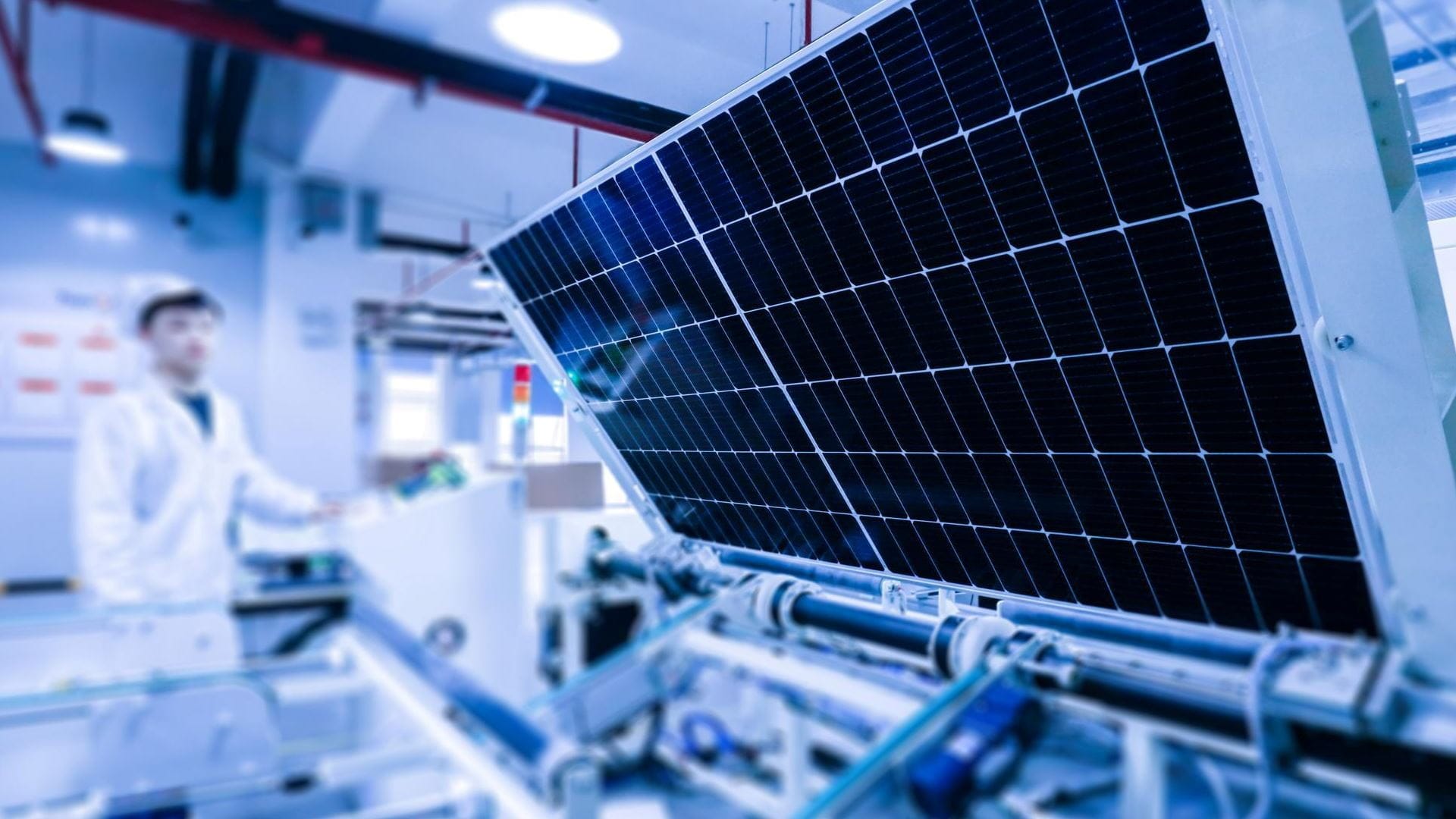
Enabling minimized dead zones and higher power efficiency
FAQs about the Jenoptik MBSS
What is a typical application for the MBSS?
Photovoltaic manufacturers must produce more cost-effectively and efficiently in order to ensure that solar cells, such as perovskite solar cells (PSC), can continue to be used as sustainable renewable energy on a large scale. The requirements for a laser system in the context of their production are very demanding: high accuracy, fast process times and high throughput rates. Jenoptik's modular beam splitting system is designed for precisely these requirements. It is used in all three process steps P1, P2 and P3 of laser structuring and can achieve extremely precise and reliable results in a significantly shorter time thanks to its parallel laser scribing. In addition, the MBSS enables very narrow and sharp P1-P2 and P3 lines. This allows a much larger “active area” and reduces the so-called “dead zone”.
The three downstream process steps of laser structuring are crucial for a consistent cell connection in the module:
- P1: Separating adjacent cells by removing the bottom electrode
- P2: Exposing the lower electrode to connect the upper and lower electrodes when the material for the upper electrode is applied
- P3: Separating neighboring cells by removing the upper electrode
The quality of the laser structuring process therefore has a direct impact on the so-called “cell-to-module losses” and thus also on the efficiency of the photovoltaic system. All the more reason to use high-performance optical solutions such as the Modular Beam Splitting System to keep manufacturing processes stable, costs low and product quality high.
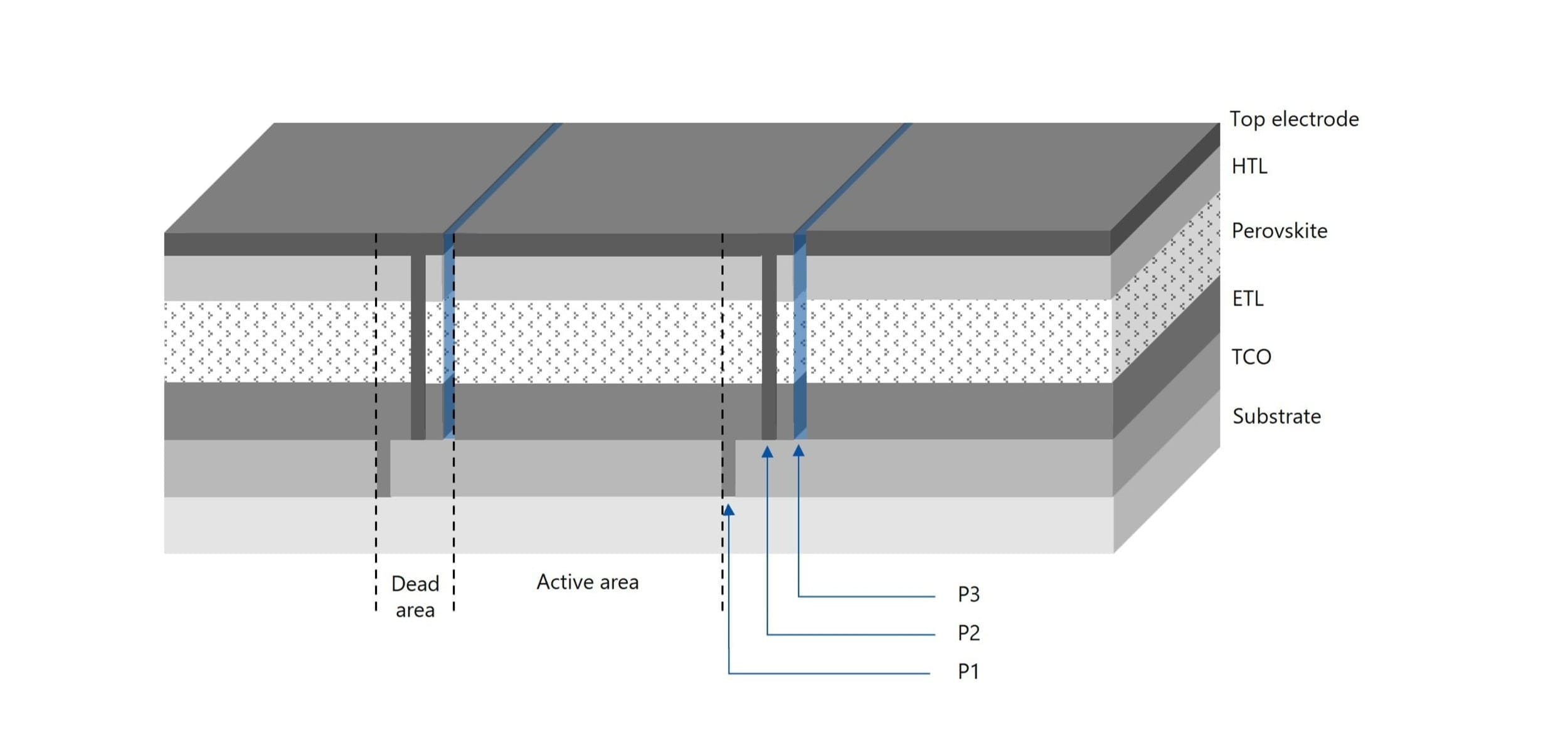
What is the benefit of MBSS if there is variation of input laser beam point direction?
For the approach with a classical beam splitter, Input laser beam tilt may cause the shift of beam incident location on each mirror, which result in variation of the pitch uniformity for output beams. See image below.
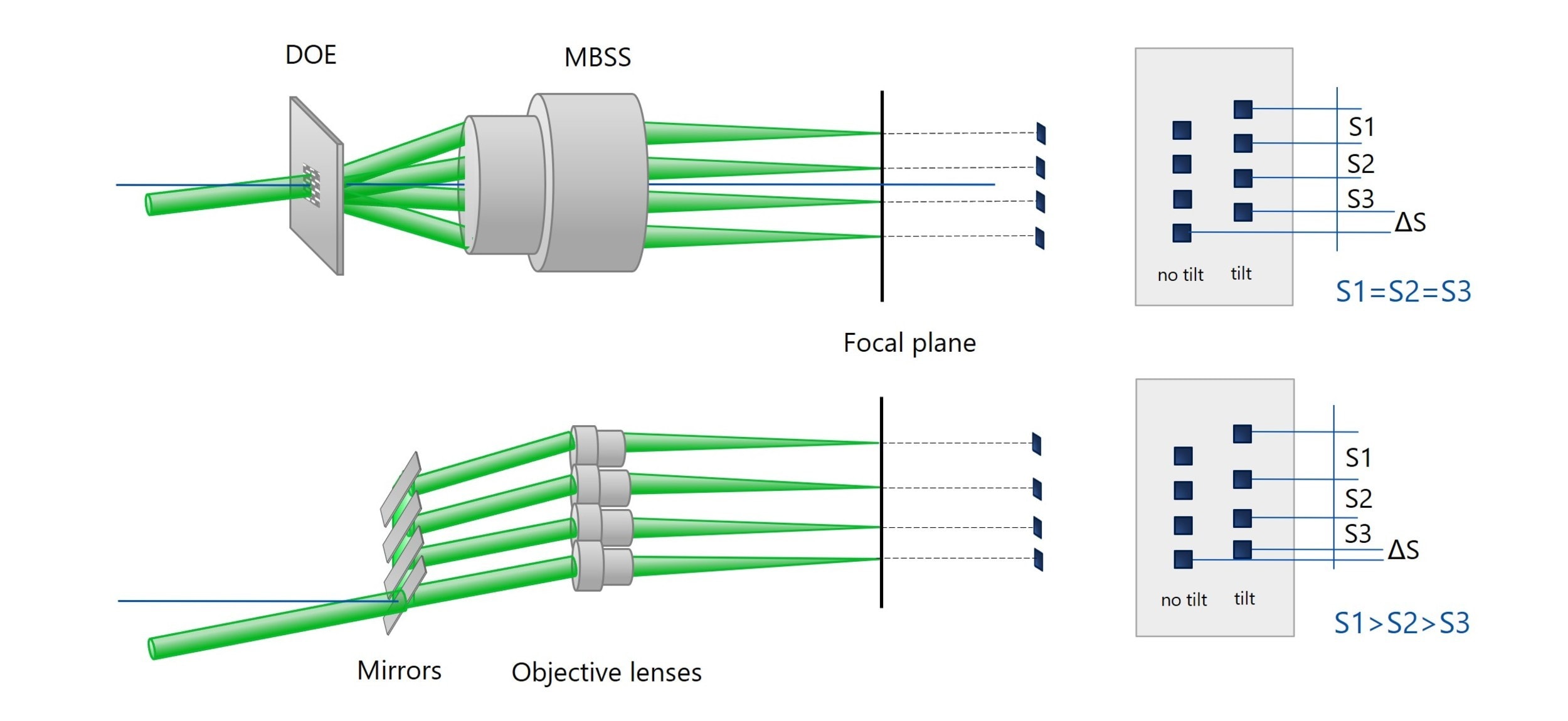
Whether customized MBSS possible, and how can the width and pitch of laser scribing line be adjusted?
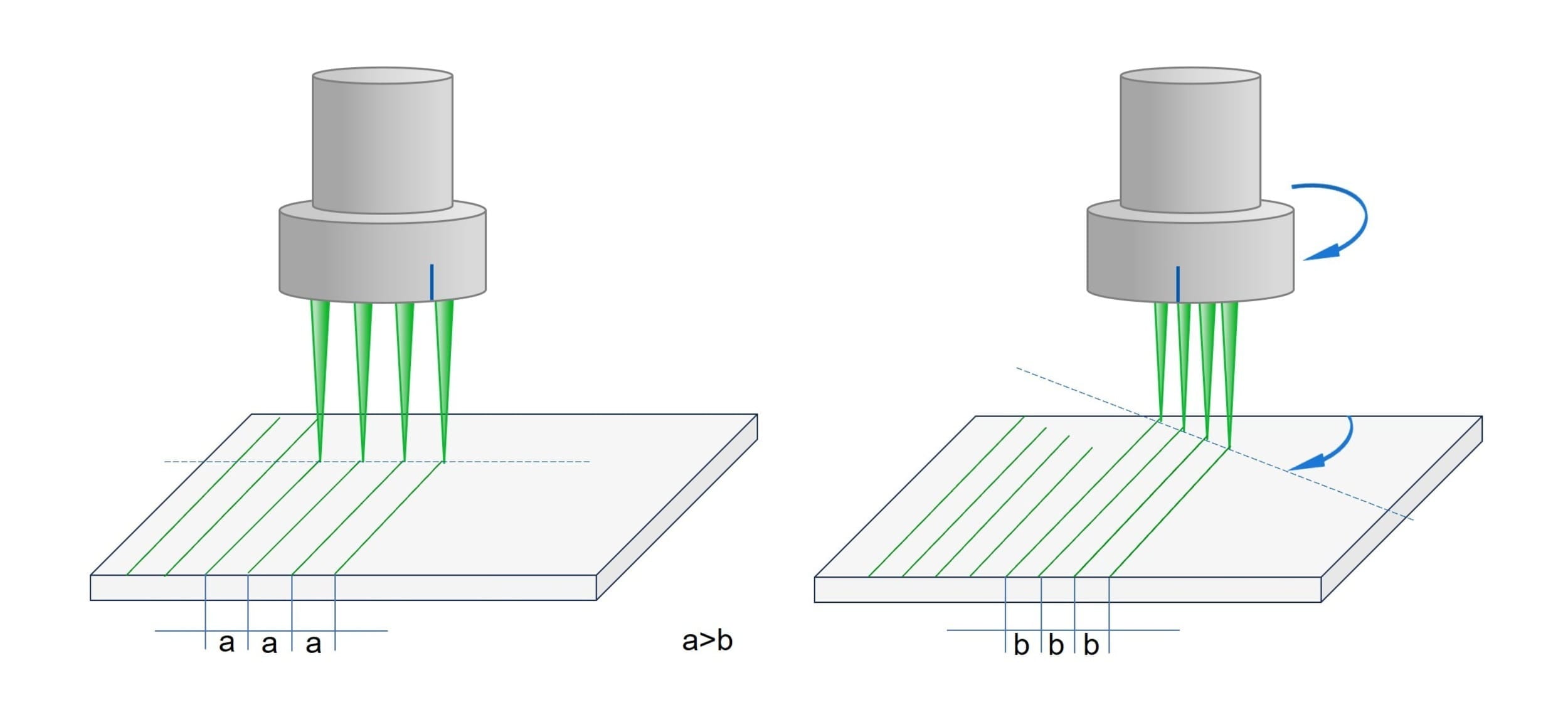
Why MBSS has the advantage of integrating DOE beam shaper for top-hat laser scribing?
A top hat beam shaper, for example, can be used to create certain shapes, like circles, squares, rectangles, lines, or others. As a diffractive optical element (DOE) the Beam shaper convert a near-Gaussian laser beam into a uniform-intensity spot with sharp edges. The result is a beam with a consistent intensity distribution across its entire surface, which is perfect for applications that require precise control over the beam's shape and intensity.
MBSS approach generates top-hat array by integrating single DOE beam shaper element. The beam shaper alignment takes only one time so much less efforts than traditional beam splitter system. In addition, MBSS multiple beams are emitted through a single optical system, therefore optimized top-hat array locate at the same focal plane, have equal top hat size with the same intensity distribution With MBSS, multiple beams are emitted through a single optical system. This makes it possible to utilize the entire depth of focus range of the lens.
Disadvantages of a classical beam shaping array with mirrors and DOEs:
- Individual DOE beam shaper for each channel need a lots of efforts for top-hat calibration.
- Objectives focal length variation results in the deviation of top hat size, top hat intensity, and the intensity distribution in top hat.
- The deviation of individual focal length may cause unequal top-hat size. Individual beamlet de-focus status result in uneven ablation effect on workpieces.
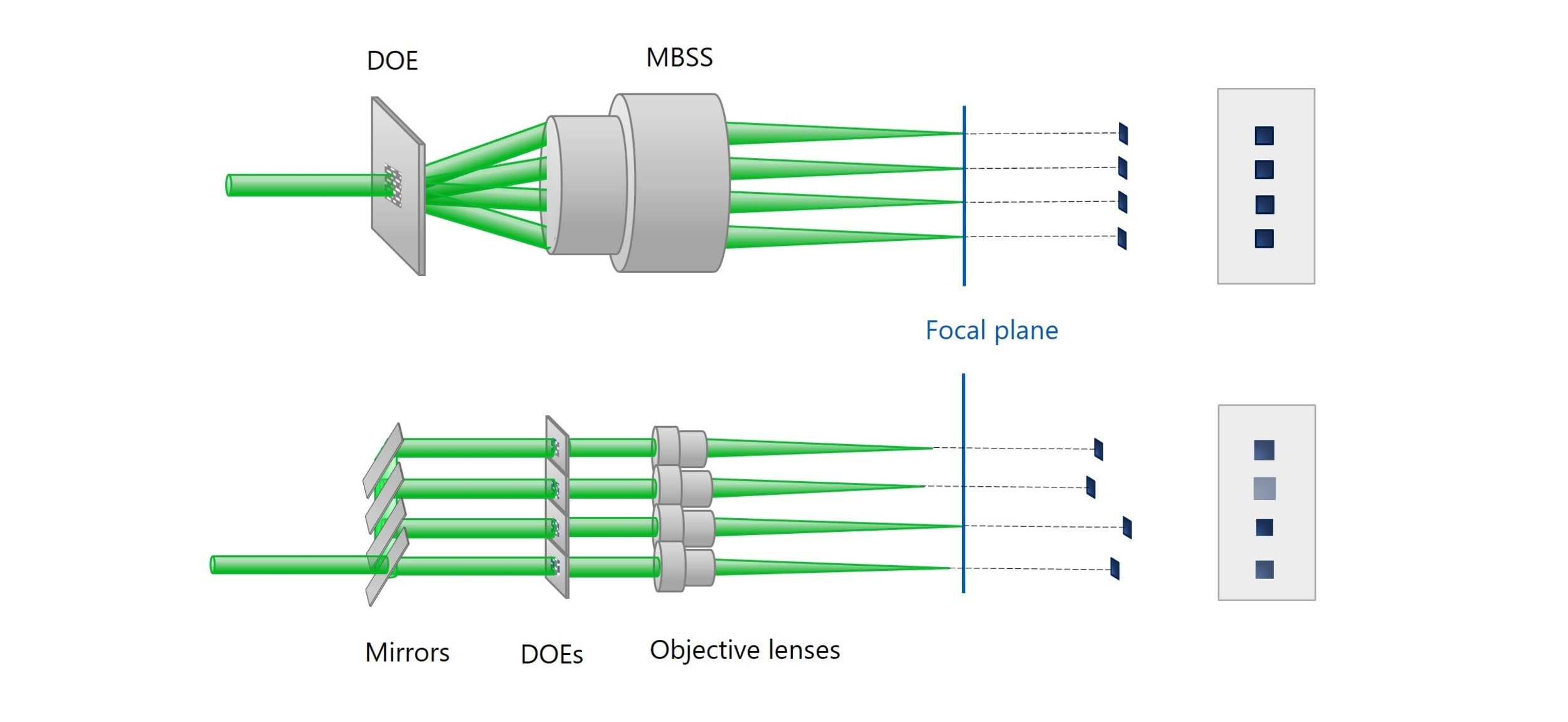
MBSS approach with one DOE for homogenous beamlets. Classical approach using beam shaping array with mirrors and DOEs.
Why MBSS can perform exceptional depth of focus (DOF) compared to traditional solutions?
With Jenoptik's Modular Beam Splitting System, multiple beams are emitted through a single optical system. This makes it possible to utilise the entire DOF range of the lens.
The MBSS solution provides a value of DOF >+/-1.0mm. This means that there is no need to integrate a focus tracking system into the laser system. In addition, the larger depth of focus (compared to existing optical setups) allows Jenoptik's MBSS to be used for both rigid and flexible perovskite solar cell laser scribing processes.
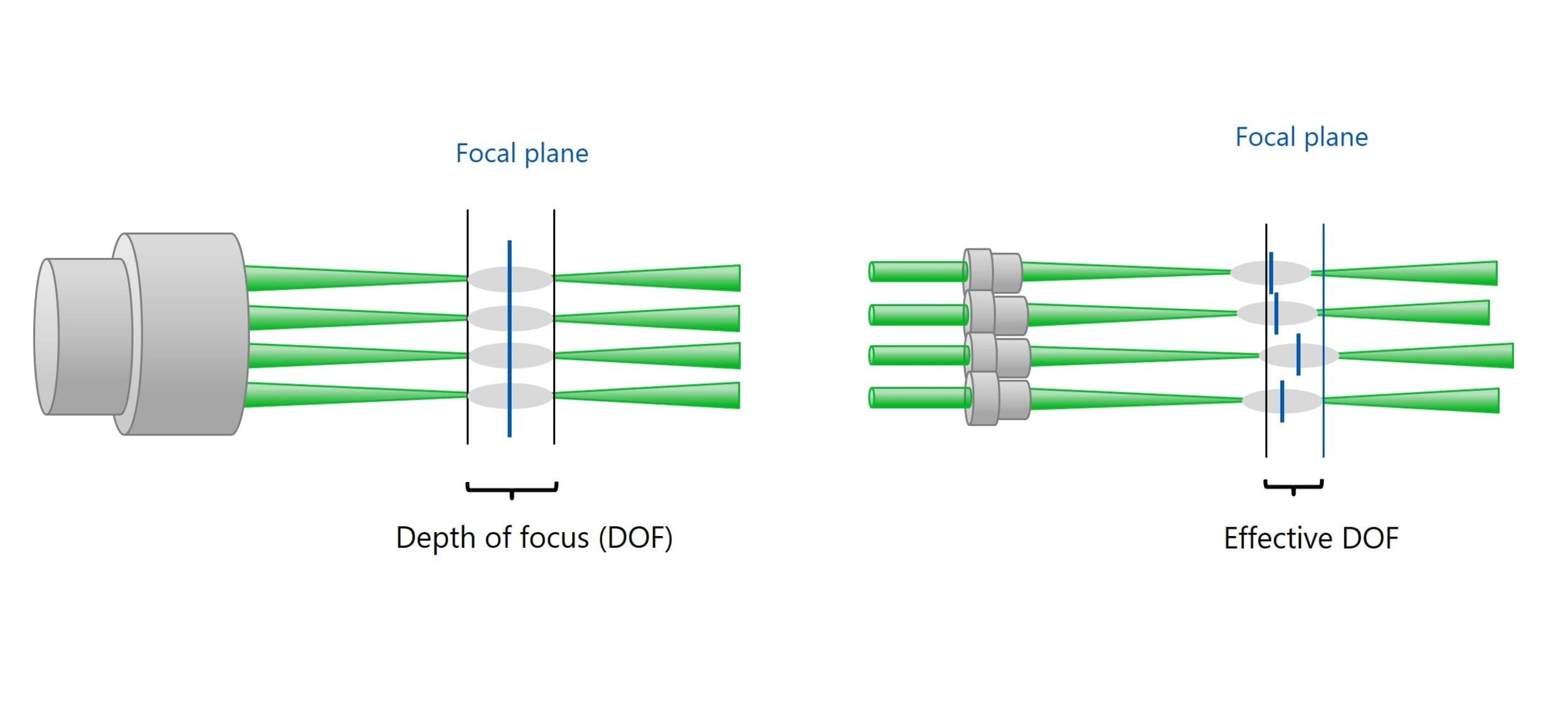
On the left: MBSS Approach with single focal plane and no significant shift On the right: For classical beam splitter system, each beamlet output comes from individual optical path. The deviation of focal length may cause the shift of focal planes result in a smaller DOF overlap area.
Whether MBSS workable for laser beam flying system? Which laser scribing technology is suitable for MBSS, input from glass side or from the film side?
Due to the light weight, MBSS can be installed flexibly in the way of laser scribing from bottom to up for inputing via glass side, or laser scribing from up to down for inputing via the film side.
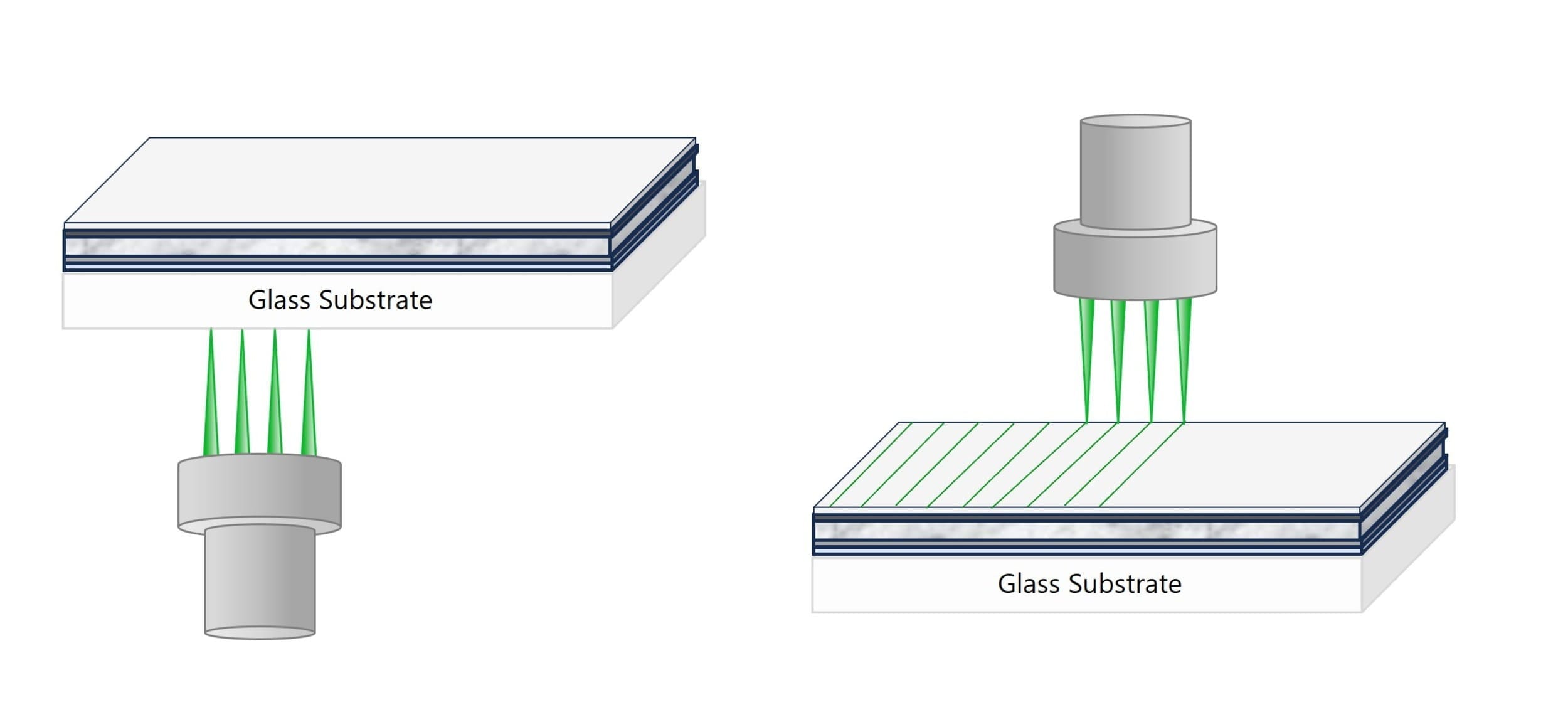
Laser input from glass side (left) and from film side from film side.
You have further questions? Contact our expert for optics and optical systems:
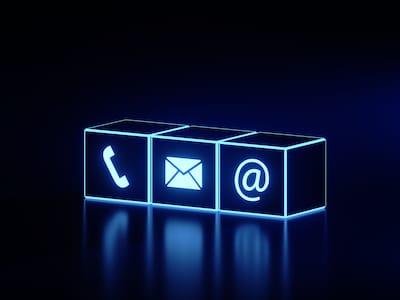
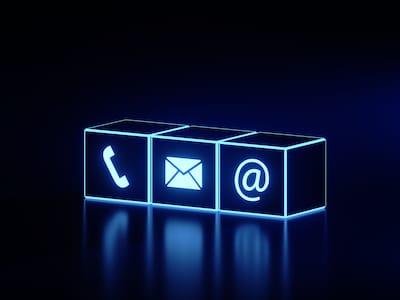
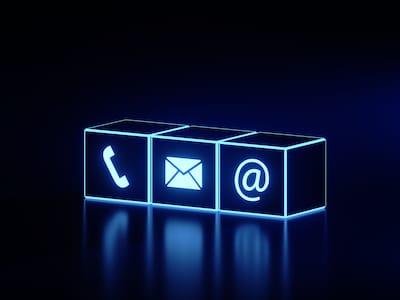
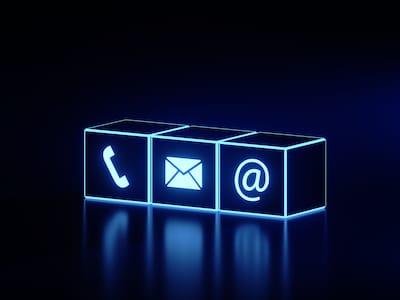
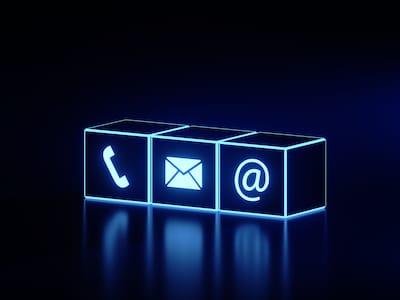
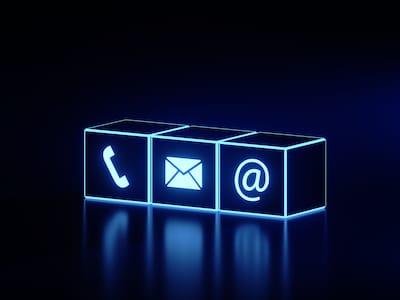
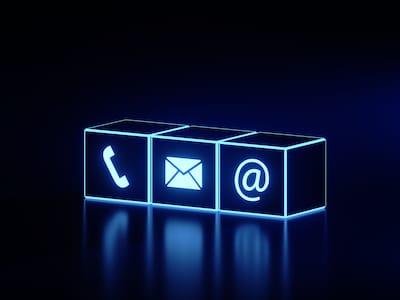