RecommendMail Facebook LinkedIn
- Tech Talk
- Smart Manufacturing
- Industry 4.0
Laser technology trends in automotive production
Laser Systems Europe (LSE) spoke with Martin Kuhnhen, head of Jenoptik’s Light & Production division, about the usage of laser technology on automotive production lines. The interview was first published in the LSE winter 2020 issue.
Jenoptik has recently won a major order for three automated production lines from Gestamp, a manufacturer of metal automotive components. The firm’s Light & Production division will design, manufacture and integrate the three lines, each of which will use different welding and laser cutting technology to help manufacture complexe car body parts for electric vehicles.
Laser Systems Europe caught up with the head of the Jenoptik division, Martin Kuhnhen, to ask him about how laser technology is being used on such production lines, as well as its current level of establishment as a manufacturing tool in the automotive industry.
What led to Jenoptik becoming an integrator of automotive production lines?
Historically Jenoptik has been in the business of standalone machines. This is because laser processing used to be conducted in such machines via individual logistics – mostly manual, sometimes with gantry solutions. Nowadays laser processing is much more integrated into production lines.
Jenoptik’s Light & Production division has acquired a few automation integration companies in North America and Spain over the past three years. We did this because we saw that there is an increasing demand for end-to-end processes from automotive manufacturers and their suppliers. Lasers are just one part of these processes, meaning that such customers are also requesting that pre- and post- laser processes are included in their production lines as well.
For example, if a production line was producing complete doorings for vehicles from press-hardened steel: while laser cutting and welding are important parts of that line, there are also conventional welding and assembly jobs before and after these processes. Historically automotive firms have had to manage several suppliers working on different pieces to bring all of this together, which can introduce logistical and timing issues.
If one entity is able to provide the equipment for all of these processes, then this takes a big headache away from manufacturers. With the disruptive change in the automotive sector, the industry is focusing on other topics now, so everyone is happy to find suppliers that can take these traditional headaches away.
Could you elaborate on this ‘disruptive change’ happening in the automotive sector?
The disruptive change refers to, for example, the fact that the automotive industry is currently having to manage the transition from conventional engines to e-mobility, the introduction of autonomous driving, or having to follow customers to Asia. There are several trends, all happening in parallel, which keeps automotive firms very busy compared to previous years.
In addition, the core competencies of automotive firms are shifting. We are seeing more and more automotive firms saying that manufacturing is no longer their most important core competence. Consequently, they need to find reliable partners to address this part of their business. This is because they still have to meet deadlines and achieve the required volumes for a runoff of a production line. Whereas automotive firms used to manage that very well themselves, they are now trusting more and more in strategic partners to do this.
Jenoptik now considers the integration of production lines to be one of its core competencies. On a customer-specific programme basis, we select the right combination of components, bring them together and manage them with the right software. It is no longer a case of just producing standalone machines. We use our own laser modules, products and software to enhance standard components from the market and secure the necessary performance.
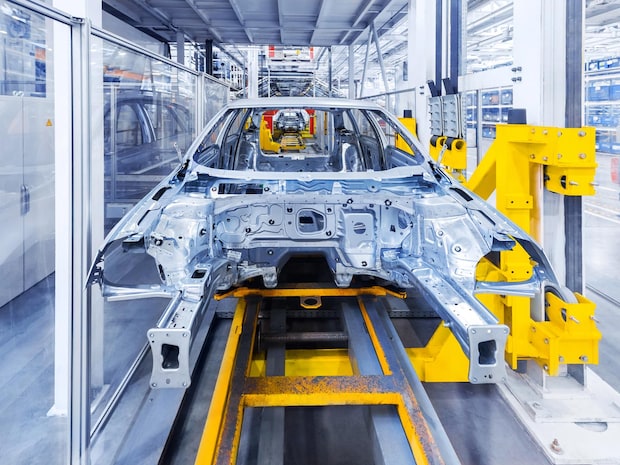
How are lasers currently being used for manufacturing in the automotive sector, what makes them suited for this purpose?
Lasers are used to cut vehicle doorings, ABC pillars or really any structural part in a car body made out of press-hardened steel. They are preferable as they offer a wear-less process – alternative mechanical tooling would wear out very quickly. This is a major market for laser processing, with many parts now coming into this corner. Lasers are also increasingly being used to cut and trim aluminum castings such as domes, cross members, rear lids, and also plastic parts – both on the interior and exterior of a vehicle.
In addition to welding and cutting, Jenoptik´s production lines perform applications such as laser marking and scoring. Airbag scoring for example is implemented on driver airbag covers and instrument panels on the passenger’s side. It has to be very precise and reliable and produce a defined break-line in such material, which allows the airbag to explode through its cover material, but only when it should – on impact. In addition, when welding components for e-mobility, for example in batteries, extreme precision is also required as you are processing components next to explosives.
Lasers also introduce a lot of flexibility to automotive manufacturing. For example if you were producing bumpers, some might require parking sensors while others will not. Whereas previously individual machines would have been required for each bumper configuration, now they could all be run through a single laser machine in a one-piece flow logic. In addition, automotive manufacturers would have to runoff production lines for producing new vehicles while keeping old equipment to produce spare parts for previous vehicles. A laser machine can instead be used to produce spare parts when required while mainly processing parts for new vehicles, minimising disruption.
Lasers will also move into new application areas in the automotive industry. We are engaged in a couple of research programmes focusing on applications where new functionality is being introduced into parts. For example there are exterior parts for autonomous vehicles that have special lighting functionality built-in, allowing the vehicle to signal to pedestrians and tell them ‘I see you.’ when a pedestrian wants to use a road crossing. In producing such parts, lasers play an important role. Such products will be seen on the streets in the next 12-18 months.
We see that process monitoring and the usage of AI is gaining increasing interest in the automotive sector, why is this?
Process monitoring is required as the materials brought into a production line have different tolerances. If output is to be increased, materials have to be measured and inspected at the beginning of the production line, and then parameters have to be changed on the fly when materials of different tolerances are introduced. Previously you would have had to take these out and say ‘I can’t process them.’, whereas now you can adjust parameters constantly, which is enabled by AI and other software-based features for process monitoring.
The inclusion of AI and process monitoring in production cells is certainly an increasing demand amongst our customers. For example, we also sold a complex line for cutting metal tubes for automotive e-drive support frames that used AI to adjust the specific cutting position by analysing the introduced material. This is a relatively new trend and we see that the usage of AI for camera-based process monitoring – both pre- and post- process – will increase in the future.
The path going forward is definitely to enhance laser capabilities with more camera based inspection and AI usage in order to make the adjustment of process parameters easier on the fly. That will be a big step going forward.
Do many more automotive firms still need to make the switch to laser technology?
Certainly. In the automotive industry, a large number of manufacturers still need to adopt laser processes. If you take laser cutting of press-hardened steel for example, three automotive suppliers currently dominate the market. They process approximately 70 per cent of all the parts. Why is that the case? This is because laser processing is a complex process. They invested early in the game and increased their knowhow about it. By taking on the whole integration process ourselves, firms like Jenoptik can reduce the barriers to adopting laser processing, enabling more and more smaller automotive manufacturers to ‘join the family’ as it were.
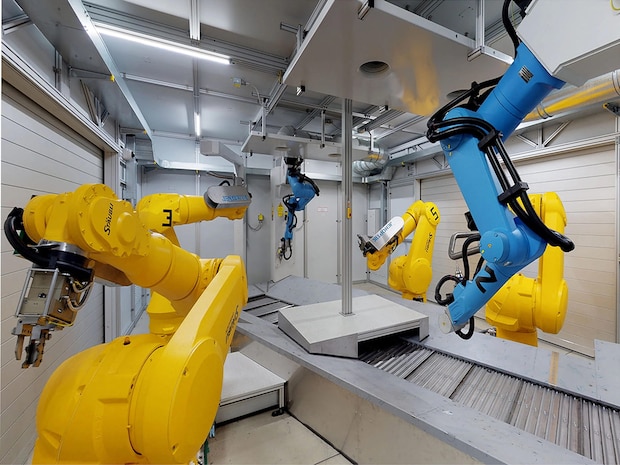
Lasers in the visible wavelength are increasingly being considered for e-mobility fabrication, will Jenoptik be keeping an eye on this technology?
We appreciate the technical benefits of green or blue lasers when welding material like copper or aluminum and in general, we are open to integrate them in our automation lines if specified. Nevertheless, our automotive customers are clearly addressing the economic aspect as well and here infrared single mode lasers sources combined with intelligent process parameters and laser beam shaping have major benefits while providing very acceptable application results.
And finally, do you believe other manufacturers of laser equipment will shift to also become integrators, as Jenoptik has done?
As of today most of the laser industry is still focusing on individual processing heads, laser sources or turnkey systems. However, we clearly see the automation and integration of laser technology will become a trend. We constantly improve our own competence to stay ahead of the game and have received very positive feedback from our customer base already.
The three production lines we are currently producing for Gestamp, which include 20 laser cutting modules, represent a significantly larger volume for Jenoptik in comparison to our traditional projects.
This article was originally published in Laser Systems Europe.